Reduce-reuse-recycle is a mantra for the times, and one that Dairyland is committed to following as much as possible in our business operating practices. For instance, the coal combustion process used to generate electricity at Dairyland’s John P. Madgett (JPM) station creates an ash byproduct. Dairyland has a strong history of recycling the majority of its fly ash annually.
Benefits of Dairyland’s ash recycling program
For each ton of coal Dairyland burns to produce electricity, approximately 5 percent - 100 pounds - results in an ash byproduct.
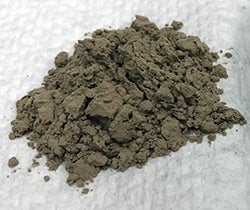
- 80 percent of this ash byproduct is referred to as fly ash, a light powdery substance captured in the emission control systems at the power plant;
- 20 percent is bottom ash, a coarse granular material collected at the bottom of the coal furnace;
- Both consist of compounds commonly found in natural clays and limestone, and are the major components of Portland cement;
- Dairyland also markets its fly ash to pipe manufacturers for use in underground piping.
Using coal combustion byproducts to replace the natural clay and limestone in the manufacturing of Portland cement is the most common recycling option used at Dairyland, with benefits for both business and the environment.
- Most concrete today in the Driftless Region is 20 percent fly ash, contributing to stronger, less permeable concrete, at a lower price.
- Fly ash is cheaper than Portland cement. Consumers save money when building roads, bridges, buildings and other community projects with concrete that contains fly ash.
- By using a recycled product, less virgin clay and limestone are extracted from quarries, which results in a reduction in carbon dioxide emissions (CO2).
- Fuel costs are lower for the cement manufacturer: Fly ash doesn't need to be “preheated” since it was already heated during the coal combustion process. This correlates with a major air-quality benefit of using fly ash in place of Portland cement.
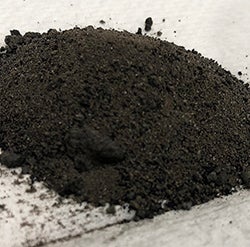
Dairyland also recycles bottom ash as a substitute for crushed rock or sand in road construction. This reduces the need to quarry rock for these purposes.
Finally, Dairyland’s ash recycling program lessens the amount of product safely stored in a landfill facility near Alma, Wis.
In the years Dairyland couldn't recycle all of its fly ash, any remaining dry fly ash was conditioned to achieve optimum moisture content in order to prevent dusting. It is then delivered by truck to the landfill storage cell. The ash is carefully compacted to construct a structure that will resist accumulation of additional moisture. In fact, the fly ash itself is somewhat like cement, which adds to the stability of the landfill storage cell.
Building Stronger Roads and Sidewalks
In 2023, Dairyland upgraded its precipitator equipment at JPM, which more than doubled the amount of fly ash collected in the combustion process. Later that summer, JPM's fly ash was used in a major road construction project near Dairyland's La Crosse headquarters when roundabouts were added on South Ave., and Mormon Coulee Road. Recycled fly ash has also been used in the construction of two wind turbine projects in southern Minnesota.
Major highway projects in Wisconsin have also utilized Dairyland's dry sorbent injection (DSI) material as a binder in stone matrix asphalt (SMA) projects for building/replacing interstate surfaces. Every bit of recycled material from Dairyland facilities saves members money and avoids the use of raw materials.
Hwy. 35 and Hwy. K near Genoa, and Hwy. 35 to Alma contain bottom ash, utilized as a “surface coarse” gravel overlay material, which “sparkles” more than standard road overlay. The bottom ash material provides better traction, is very durable and doesn’t break windshields as readily as standard gravel. It also melts ice faster … a real bonus for winter driving.